Introduction: What is Carding in Fiber Preparation?
Carding is a critical step in the preparation of fibers for spinning. It involves a mechanical process used to separate, clean, and align fibers to remove impurities, making them ready for the next stage of yarn production. The carding process is commonly used with natural fibers like cotton, wool, and flax, as well as synthetic fibers, to ensure that the fibers are properly aligned and free from debris.
In this article, we will explore what carding is, why it’s important in textile manufacturing, and the process it entails.
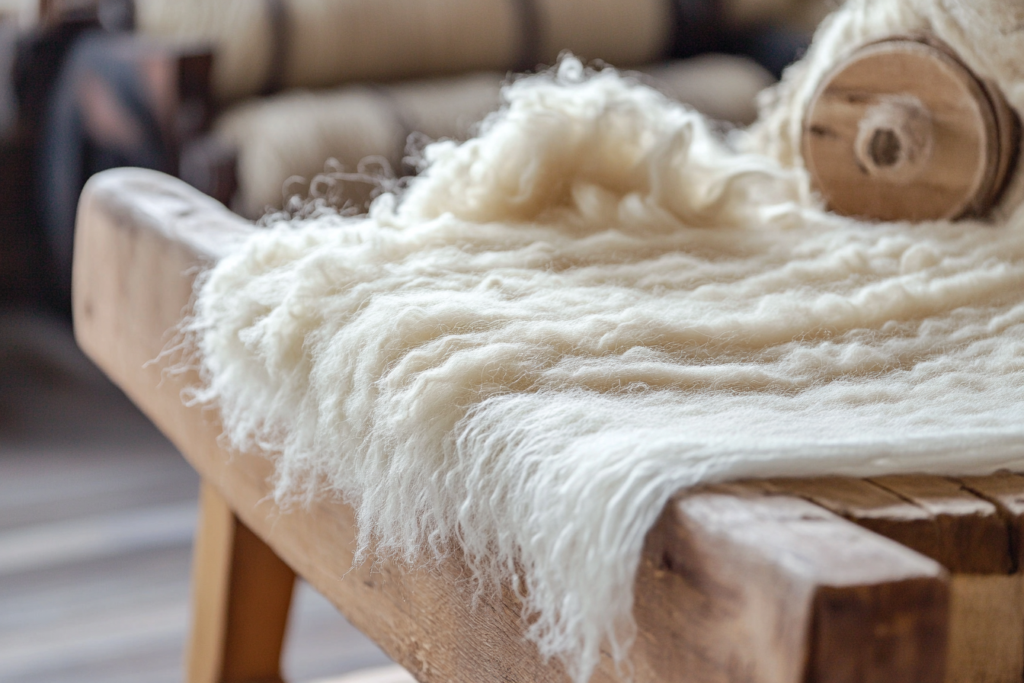

The Importance of Carding in Textile Manufacturing
Carding is vital because it ensures the quality and consistency of the fibers used to create yarn or fabric. Before carding, fibers tend to be tangled, uneven, and contain various impurities like dirt, grease, or shorter fibers. The carding process helps in achieving the following:
- Separation of Fibers:
- Carding separates the individual fibers from each other, which is crucial for ensuring that they are evenly aligned when spun into yarn. Without proper separation, the yarn could end up uneven or weak.
- Removal of Impurities:
- Fibers often contain impurities such as dirt, oil, or vegetable matter, especially when sourced from natural materials. Carding removes these impurities, ensuring the final product is clean and of high quality.
- Uniformity and Consistency:
- The process helps to achieve uniform fiber distribution, which is essential for creating strong and smooth yarn. Consistent fiber alignment also improves the finished fabric’s quality, texture, and durability.
- Preparation for Spinning:
- After carding, the fibers are prepared for the spinning process. The carded fibers are typically formed into a loose, continuous web or sliver that can be fed into the spinning machine.
The Carding Process: Step-by-Step
The carding process generally involves several steps that prepare the fibers for spinning. Here’s a breakdown of the process:
- Feeding the Fibers:
- The raw fibers, often in the form of a loose mass, are fed into a carding machine. These fibers are then pulled into the machine by a set of rollers.
- Breaking Up Clumps:
- The machine uses a series of wire-covered rollers to break up any clumps or tangled masses of fiber. The rollers rotate at different speeds to gently open up the fibers.
- Cleaning and Separation:
- As the fibers move through the machine, they pass over a series of combs or brushes that remove dirt, vegetable matter, and shorter fibers. These impurities are discarded, and the remaining fibers are aligned.
- Carding:
- The fibers are then passed through a series of rotating drum-like devices known as carding drums or cylinders. These drums have wire teeth that further separate and align the fibers, resulting in a fine, even layer of carded fiber.
- Formation of a Sliver:
- After carding, the aligned fibers are gathered into a loose, continuous strand called a sliver. This sliver is then collected and ready for spinning.
Types of Carding Machines
Several types of carding machines are used in the textile industry, each suited for specific types of fibers and production volumes. Here are the most common types:
- Flat Carding Machine:
- This is the most widely used machine for carding natural fibers like wool, cotton, and flax. The flat carding machine uses a series of rotating flat surfaces with fine wire teeth to separate and clean the fibers.
- Roller Carding Machine:
- A roller carding machine is typically used for fibers that are more difficult to card, such as synthetic fibers or blends. It uses a series of rollers to handle the fibers and remove impurities.
- High-Speed Carding Machine:
- As the name suggests, these machines are designed for high-volume production. They are typically used in large-scale textile mills and can process a significant amount of fiber quickly.
The Role of Carding in Fiber Types
Different types of fibers require different handling during the carding process. Here’s a look at how carding is applied to different fibers:
- Wool:
- Wool fibers are naturally crimped, which makes them somewhat easier to card. Carding helps to align the fibers, remove impurities, and separate any shorter fibers that could weaken the finished yarn.
- Cotton:
- Cotton fibers are shorter and finer, making them more challenging to card. Carding helps to separate the fibers and remove the sticky impurities naturally present in cotton. Cotton also requires a high level of precision during the carding process to ensure the yarn is consistent.
- Synthetic Fibers:
- Synthetic fibers like polyester or nylon can also be carded, though the process differs slightly from natural fibers. The fibers are generally finer and more uniform, so the focus is more on separating any clumps and aligning them for spinning.
- Blended Fibers:
- Many fabrics are made from a blend of natural and synthetic fibers. In these cases, carding ensures that both fiber types are evenly distributed and prepared for spinning.
Carding and Its Impact on Final Fabric Quality
The quality of the final fabric depends largely on the quality of the carding process. An efficient and thorough carding process results in smooth, high-quality yarn that produces durable and attractive fabrics. If the carding process is rushed or improperly done, it can lead to poor yarn quality, such as uneven texture or weak spots.
Moreover, the type of fiber being carded and the way it’s carded significantly influences the texture and appearance of the finished fabric. Carding can also affect the fabric’s softness, durability, and even its ability to be dyed effectively.
Conclusion: The Essential Role of Carding in Textile Manufacturing
Carding is an essential process in the textile industry, particularly in the preparation of fibers for spinning. It helps to remove impurities, align fibers, and ensure uniformity, all of which contribute to the quality and consistency of the final product. Whether working with cotton, wool, or synthetic fibers, carding ensures that the fibers are ready for the spinning process and ultimately the creation of high-quality fabric.
By understanding the role of carding in textile manufacturing, designers and manufacturers can ensure that their fabrics are strong, consistent, and ready for the next stage of production.