Introduction: The Importance of Fabric Layout
In garment manufacturing, fabric layout refers to the arrangement of pattern pieces on a fabric before cutting. The goal is to maximize fabric utilization, reduce waste, and improve cost efficiency. The layout is critical in optimizing fabric usage, ensuring that the pattern pieces fit together in a way that minimizes scrap and ensures the fabric is cut to its full potential.
Effective fabric layout can result in significant savings, especially when dealing with expensive or limited fabric supplies. Whether you are working with a basic cotton or luxurious silk, a well-planned fabric layout can improve the efficiency of the cutting process and, ultimately, the overall production process.
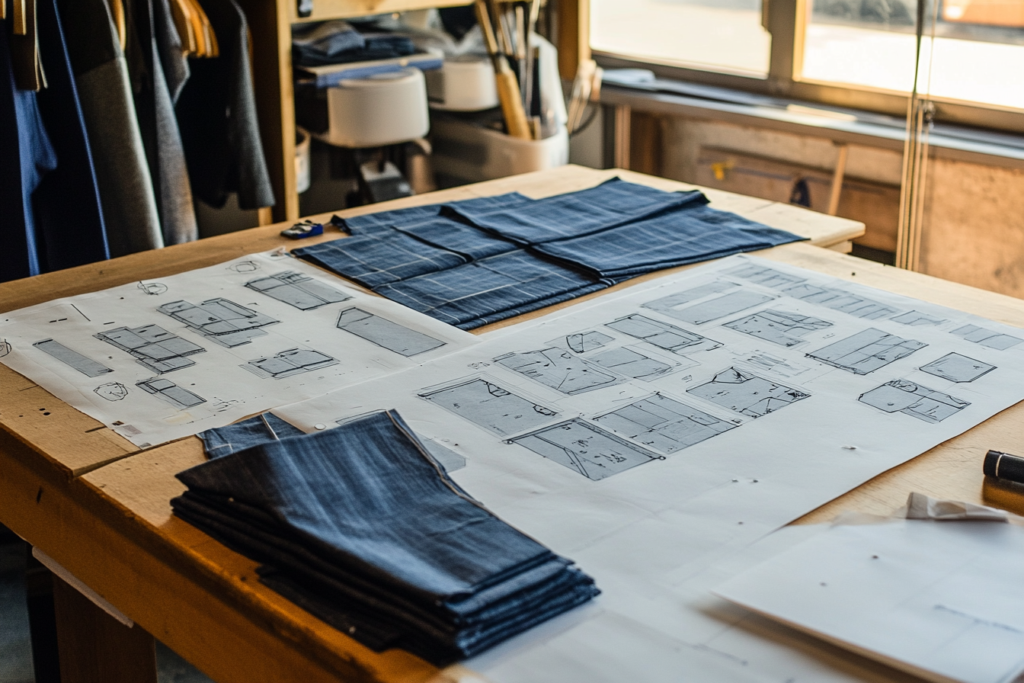
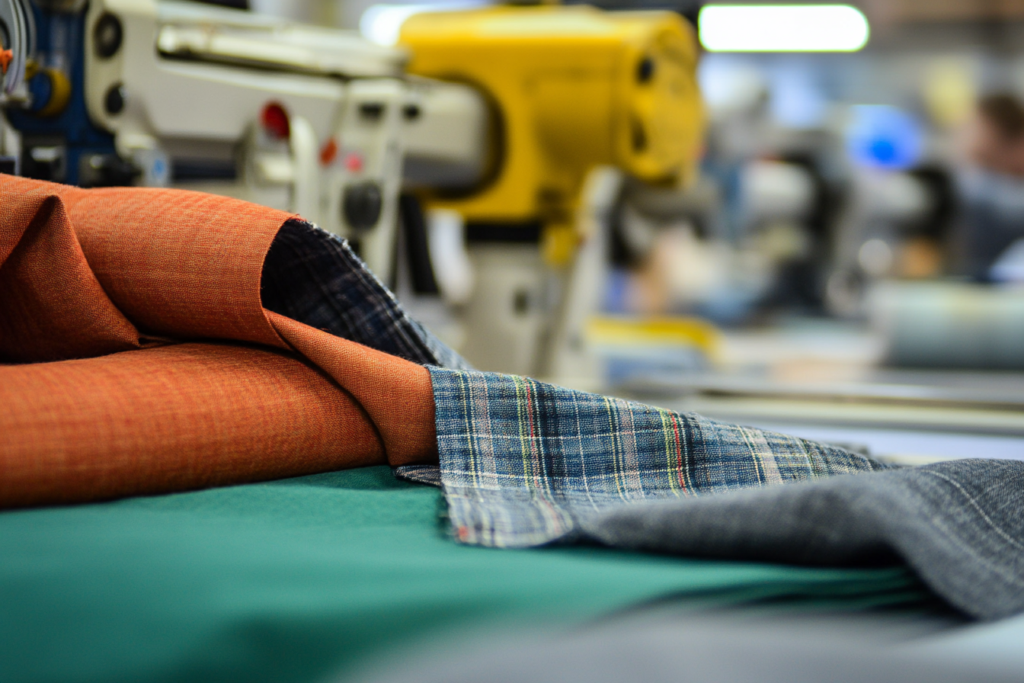
Types of Fabric Layout
- Single-Layer Layout:
- In this type of layout, fabric is spread out in a single layer, and pattern pieces are arranged on it accordingly. This layout is commonly used for fabrics with patterns or prints that need to be aligned carefully (e.g., stripes or floral patterns).
- It is more time-consuming and often used when working with delicate or high-value fabrics where careful cutting is required.
- Multiple-Layer Layout:
- Multiple layers of fabric are stacked on top of each other, allowing for several pattern pieces to be cut at once. This is a faster and more efficient method compared to single-layer cutting.
- Multiple-layer layouts are used in mass production and for fabrics that do not require precise pattern alignment, such as solid-colored fabrics or fabrics with no directional print.
- Grain Layout:
- Grain layout refers to the alignment of the pattern pieces in relation to the fabric’s grain. The fabric’s grain (lengthwise, crosswise, or bias) affects the way the garment drapes and fits.
- Pattern pieces must be laid out according to the grainline indicated on the pattern to ensure proper fit and appearance. Misalignment can result in distortion of the garment and poor performance.
- Marker Making:
- Marker making is the process of arranging the pattern pieces on the fabric in a way that minimizes fabric wastage. It involves creating a “marker,” which is essentially a plan or guide for cutting the fabric.
- Marker making can be done manually or with the help of computer-aided design (CAD) software, which helps designers create optimal layouts for large fabric rolls. Advanced marker-making software can further maximize fabric utilization by considering fabric characteristics, such as stretch, pattern repeat, and fabric width.
Factors Affecting Fabric Layout
- Fabric Width:
- The width of the fabric plays a significant role in the layout process. Wider fabrics may require fewer layers to achieve the same number of pattern pieces, reducing time and labor. Narrower fabrics, however, require more layers or smaller pattern pieces to make the most of the available space.
- Fabric Direction:
- Some fabrics, such as those with directional prints or patterns, must be laid out carefully to ensure that the design aligns correctly. For example, fabric with a one-way print needs to have all pattern pieces aligned in the same direction, which may require more careful planning and adjustment.
- Pattern Shape and Size:
- The shape and size of the pattern pieces influence how they fit together on the fabric. Smaller, more uniform pattern pieces can fit together more easily, reducing fabric waste. In contrast, larger or irregularly shaped pieces may create more space between them, leading to increased fabric waste.
- Fabric Type and Properties:
- Certain fabric types, such as stretch fabrics or those with nap (e.g., velvet or corduroy), require extra consideration in layout. These fabrics may need to be laid in a particular direction to ensure proper alignment, stretch, and visual appeal.
- Cost Considerations:
- The primary objective of fabric layout is to minimize fabric wastage, which directly impacts material costs. A careful layout design can help avoid unnecessary cuts and excess fabric, lowering overall production costs. In the fashion industry, fabric can represent a significant portion of the production cost, making efficient fabric layout an important factor.
Best Practices for Effective Fabric Layout
- Plan Ahead:
- A detailed and well-thought-out fabric layout plan should be prepared before starting the cutting process. This includes determining the most efficient layout based on fabric width, pattern shape, and fabric type.
- Use CAD Software:
- For large-scale or complex production, using Computer-Aided Design (CAD) software can greatly enhance the efficiency of fabric layout. CAD systems allow for precise planning and optimization, reducing fabric waste and cutting time.
- Consider Fabric Usage:
- When creating the fabric layout, take into account any fabric defects or imperfections. This helps ensure that the pattern pieces are placed strategically to avoid wasting fabric in areas where defects may be present.
- Grainline and Pattern Placement:
- Always align pattern pieces with the grainline specified on the pattern. Proper alignment ensures that the fabric will behave as expected, with the correct drape and fit. Additionally, carefully consider the placement of notches, zippers, and other design elements.
- Optimize Layout for Mass Production:
- In mass production, the goal is to maximize efficiency and reduce cutting time. Grouping similar pattern pieces and arranging them in an organized manner can speed up the cutting process and save valuable time and fabric.