The Essential Technical Source for Designers: A Guide to Effective Design and Production
- Body Measurements and Size Chart (5)
- Clothing Glossary (275)
- design and develop (14)
- Edge processing (30)
- Fabric (0)
- Fasteners (0)
- Fitting and Trying On (0)
- Labels and packaging (0)
- Sewing (0)
- Shaping and support technology (0)
- Structural lines and modeling methods (0)
- Style drawing (0)
- Tech Pack (9)
- Technical terms for garment silhouettes and details (0)
- Uncategorized (2)
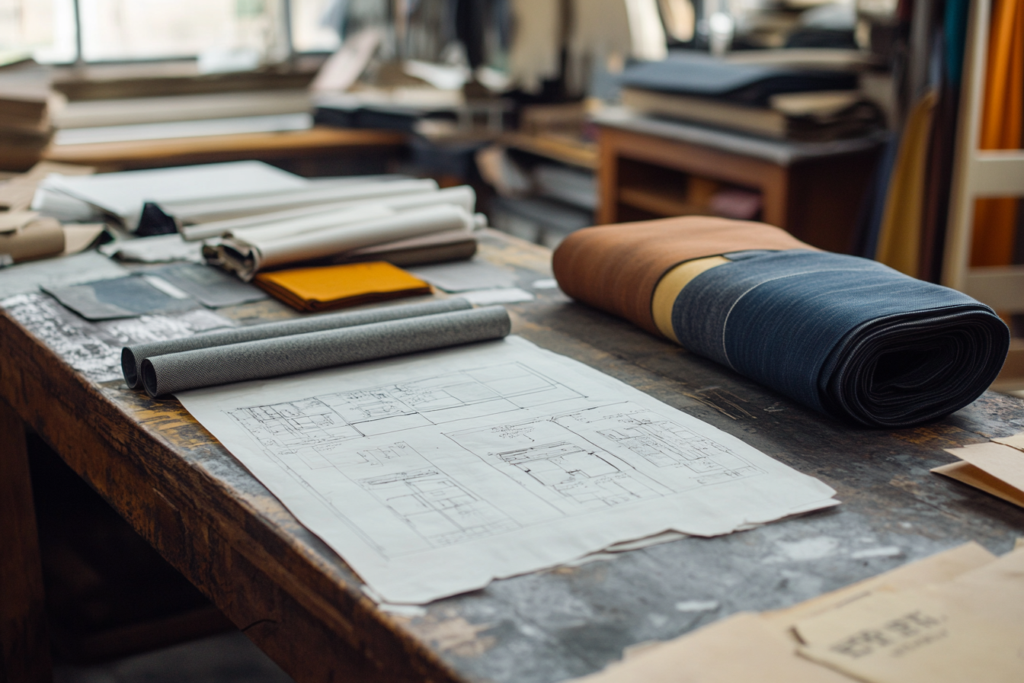

In the fashion industry, successful garment production relies on more than just creativity and aesthetics. Designers must also navigate complex technical requirements, measurements, materials, and production processes. This is where a technical sourcebook becomes an invaluable tool for designers. A technical sourcebook is a comprehensive guide that consolidates all the critical information needed to bring a designer’s vision to life, from initial concept to final production.
What is a Technical Source for Designers?
A technical source for designers is a detailed reference guide that contains all the necessary technical specifications, design standards, and production guidelines for creating garments. It serves as a bridge between the designer’s creative ideas and the manufacturer’s ability to execute those ideas accurately.
This document helps ensure that the garment is not only visually appealing but also functional, manufacturable, and consistent in quality across production runs. It typically includes information on pattern-making, garment construction, materials, sizes, grading, stitching, finishes, and labeling. The sourcebook is a crucial tool for designers to communicate their concepts clearly to manufacturers and ensure that every aspect of the garment meets the desired specifications.
Why is a Technical Source Important for Designers?
A technical sourcebook is an essential resource for designers for several reasons:
1. Streamlining the Design-to-Production Process
The process of turning a design into a final product involves multiple stages, from sketching and fabric selection to production and quality control. Without a clear, comprehensive set of instructions, miscommunication can lead to errors, delays, and poor-quality garments. The sourcebook helps designers create a cohesive, structured document that outlines every aspect of the design, which the manufacturer can follow step-by-step.
2. Ensuring Consistency Across Production Runs
For designers working with a manufacturer to produce a collection or a line of garments, consistency is key. A technical sourcebook ensures that every garment in a collection maintains the same high standard, whether it’s the first sample or the hundredth unit. By standardizing measurements, stitching techniques, and fabric specifications, the sourcebook helps reduce the risk of variations or mistakes during production.
3. Facilitating Communication with Manufacturers
Designers often work with different manufacturers, and clear communication is essential to ensure that their designs are accurately translated into finished garments. A well-organized technical sourcebook eliminates ambiguity by providing precise guidelines, such as stitching types, fabric choices, fit specifications, and construction techniques. This makes it easier for manufacturers to understand the designer’s intentions and avoid costly mistakes.
4. Improving Efficiency
By centralizing all critical design information in one document, the sourcebook can significantly improve workflow. Designers can quickly access material specifications, construction instructions, and other details without needing to refer to multiple sources. This efficiency speeds up the sample-making process, sample approvals, and production timelines, helping to meet market deadlines.
5. Reducing Production Costs
The more detailed and accurate the technical sourcebook, the fewer revisions and changes are needed during production. This reduces the number of sample iterations and prevents mistakes that could lead to waste, making production more cost-effective. The sourcebook allows for smoother operations and fewer delays, which in turn reduces labor and material costs.
Key Components of a Technical Source for Designers
A technical sourcebook serves as a comprehensive guide that covers every aspect of garment design and production. Below are the essential components that a typical technical sourcebook will include:
1. Design Overview and Concept
This section includes a general description of the design concept and vision. It sets the tone for the garment and explains the designer’s creative intentions. This includes:
- Design sketches or technical flats: Detailed 2D representations of the front, back, and side views of the garment, showing every key design element (e.g., neckline, waistline, cuffs).
- Mood board or inspiration: Visual references that inspire the design, such as fabric samples, color palettes, and style references.
- Target market: The intended consumer demographic, which helps define fit, fabric choice, and overall style.
2. Materials and Fabrics
The fabric and materials used are crucial to the garment’s look, feel, and functionality. This section outlines:
- Fabric types and specifications: Describes the fibers, textures, and properties of the materials used (e.g., cotton, wool, silk, synthetic blends).
- Swatches or fabric samples: Small pieces of fabric or color swatches that represent the actual material to be used.
- Fabric weight and performance: Information on the weight (e.g., light, medium, heavy) and performance characteristics of the fabric (e.g., breathable, stretch, durable).
- Trims and accessories: Details about buttons, zippers, labels, and any other finishing elements that complete the garment.
3. Size Specifications and Grading
Size is a critical element in the garment design process. This section outlines the following:
- Size charts: Detailed measurements for each size (XS, S, M, L, etc.), covering key areas such as bust, waist, hip, inseam, and sleeve length.
- Grading rules: Guidelines on how the pattern will be adjusted to accommodate different sizes while maintaining proportion and fit.
- Fit specifications: Descriptions of the intended fit (e.g., slim fit, loose fit, regular fit) and any special requirements for how the garment should drape or hug the body.
4. Construction and Stitching Methods
The construction of the garment is as important as its design. This section includes:
- Seam types: Describes the stitching methods to be used for different parts of the garment (e.g., French seams, overlock, double-needle, and topstitching).
- Stitching instructions: Specifies the stitch type (e.g., straight, zigzag) and thread type (e.g., polyester, cotton) for each step of the garment’s construction.
- Seam allowances: Details the amount of fabric to be included in seams to ensure a proper fit and ease during construction.
- Special construction techniques: Includes any unique or intricate stitching required for the design (e.g., embroidery, appliqué, pleating).
5. Fitting and Sample Evaluation
Fitting is one of the most crucial steps in the design process. This section includes:
- Fitting session records: Documentation of the garment’s fit on a model or fit mannequin, with notes on areas that need adjustment (e.g., tightness, length, comfort).
- Sample evaluation: Feedback on how the garment matches the designer’s vision, including details on comfort, functionality, and design accuracy.
- Modifications and adjustments: Recommendations for changes that will improve the garment, such as altering measurements, adding ease, or changing the stitching technique.
6. Labeling and Packaging
This section outlines the labeling and packaging requirements for the garment. This includes:
- Labeling instructions: Specifies the types of labels to be used, such as care labels, size labels, and brand labels. It also includes the exact placement of these labels on the garment.
- Packaging guidelines: Describes how the garment should be folded, packaged, and prepared for shipping. This includes protective measures to prevent damage, such as plastic bags, tissue paper, or cardboard inserts.
7. Production Timeline and Costing
The final section of the technical sourcebook should include:
- Production timeline: A detailed schedule outlining key milestones, from sample creation to final production and delivery dates.
- Costing details: A breakdown of the garment’s production costs, including materials, labor, trims, and any other costs associated with manufacturing.
Benefits of a Technical Source for Designers
- Improved Communication: The sourcebook acts as a universal reference document that all stakeholders—designers, manufacturers, and technical teams—can use to ensure they are on the same page.
- Increased Efficiency: With all the necessary information in one place, designers can speed up the sampling process and reduce the time spent clarifying details.
- Consistent Quality: The technical sourcebook ensures that garments are produced to the same specifications, maintaining consistent quality across production runs.
- Cost Control: By providing clear instructions and guidelines, the sourcebook helps prevent mistakes and unnecessary revisions, ultimately saving time and money.
- Scalability: For designers working on large collections or with multiple manufacturers, the sourcebook helps streamline production and make the process scalable.