🌸 Directional Prints in Fabric Cutting: What Designers and Manufacturers Must Know
Directional prints add uniqueness and visual charm to garments, but they also introduce complexity in fabric layout and cutting. Whether you’re working with upward floral prints or exclusive selvedge prints, understanding the orientation of designs is critical in fashion production.
🧵 What Are Directional Prints?
Directional prints are fabrics where the design has a clear orientation—typically “up” or “down.” For instance, a fabric featuring the Eiffel Tower or trees must face one direction for a visually pleasing final garment. These are known as unidirectional prints.
In contrast, bidirectional prints feature repeating motifs in multiple directions (e.g., flowers facing up and down), offering more flexibility and minimizing waste during the cutting process.
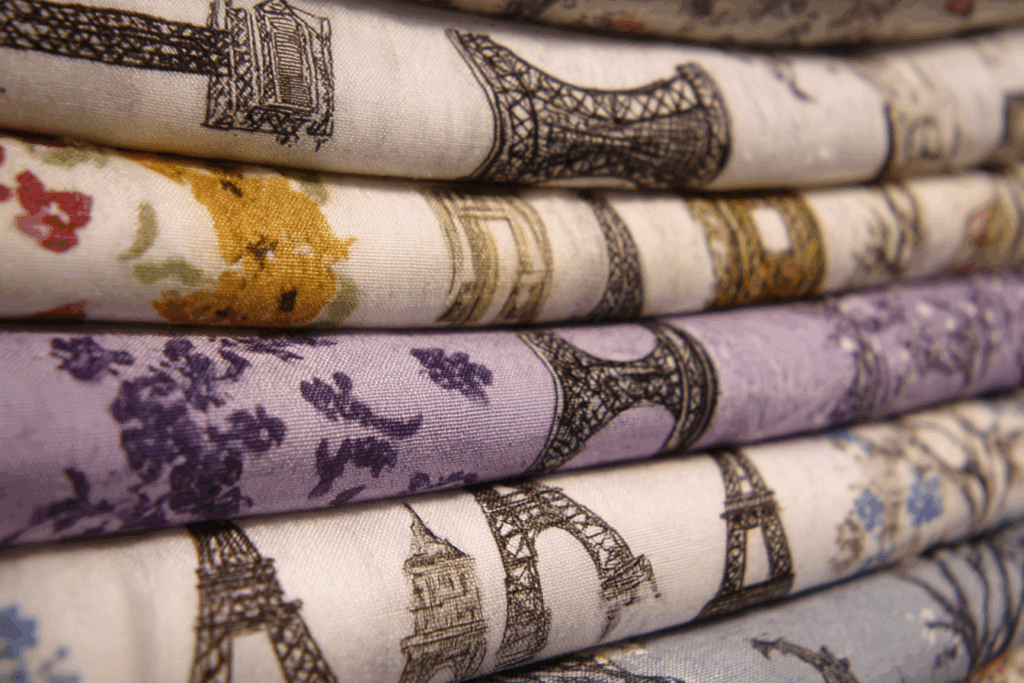
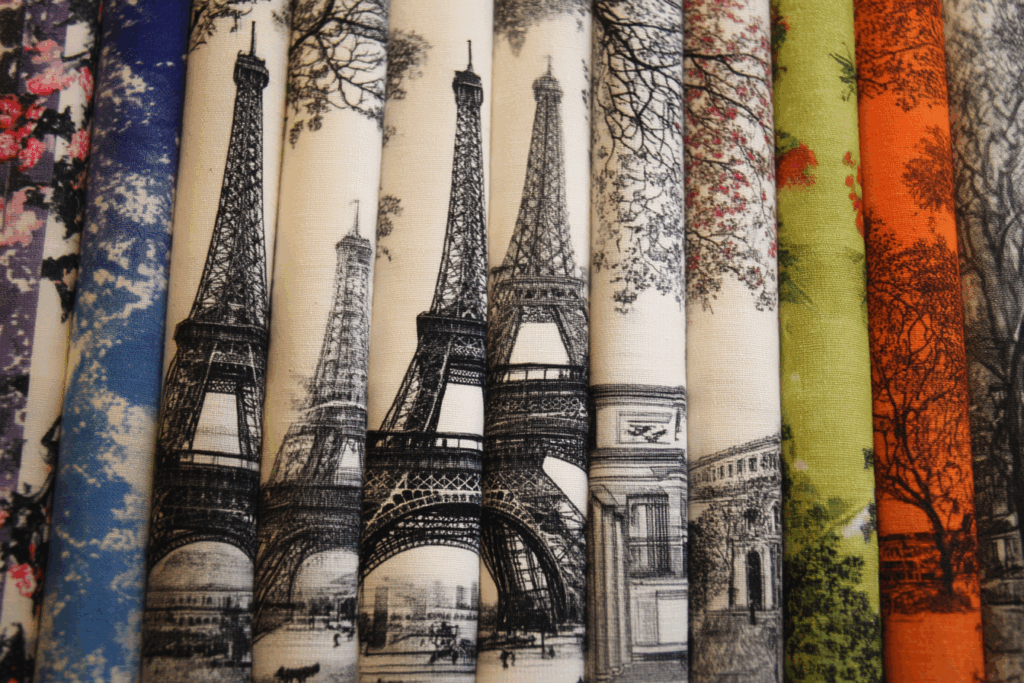
✂️ Fabric Cutting Techniques for Directional Prints
1. Unidirectional Prints
- Require all pattern pieces to be placed in the same direction.
- Typically consume 15–20% more fabric due to orientation restrictions.
- Must be accurately costed in the early design phase.
- Ideal for designs where vertical alignment matters (e.g., long dresses, tailored blouses).
📝 Example Instruction:
All flower stems must face downward. No flipped placement allowed.
2. Bidirectional Prints
- Offer more flexibility in marker layout.
- Lower fabric waste and reduced production cost.
- Best suited for mass production or cost-conscious projects.
📝 Cutting Tip:
Bidirectional prints allow two-way layout — pattern pieces can face either direction.
🎨 Special Case: Selvedge Prints
Selvedge prints have decorative designs running along the fabric’s edge. These fabrics:
- Require precise placement to preserve the design integrity.
- Often need bias cutting or special shaping methods.
- Consume more yardage and increase overall garment cost.
- Add exclusivity, often used in skirts, scarves, and couture pieces.
💡 Cutting Considerations:
- Selvedge placement must align with the garment’s silhouette.
- Bias cutting should be avoided when there is a large difference in warp and weft weights.
👗 Design Approaches for Selvedge Print Skirts
a. Graceful Layout (Figure a)
A soft, vertical drape using the selvedge as a hem detail—no harsh contrast.
b. Zigzag Hem (Figure b)
Cut on the bias to create a dynamic edge; ideal for avant-garde fashion.
c. Lace-Style Selvedge (Figure c)
Used in straight skirts with pleats—perfect for vintage or hand-woven designs.
📋 Cutting Instructions Sample (Unidirectional Layout)
XYZ Fashion Group
Pattern Cutting Guide
- Cutting Type: No fluff, one-way only
- Pattern Orientation: All pieces must face upward
- Fabric Note: Use “flower stem” as directional reference
🔑 Key Takeaways
Print Type | Cutting Direction | Fabric Waste | Design Flexibility |
---|---|---|---|
Unidirectional | One-way only | High | Low |
Bidirectional | Two-way allowed | Low | High |
Selvedge Print | Customized layout | Variable | Medium |
🧵 Conclusion
When using directional prints—especially unidirectional or selvedge prints—designers and manufacturers must carefully plan marker layouts and cutting techniques. By understanding the directionality, one can control fabric waste, optimize cost, and deliver exceptional visual results in finished garments.