Marker Making in Garment Production: A Key to Fabric Efficiency and Cost Control
Marker making is an essential process in the garment manufacturing workflow that directly affects fabric utilization, cost, and production efficiency. It involves laying out pattern pieces for cutting in a way that minimizes fabric waste and ensures alignment with fabric properties such as grain direction and pattern repeat. A well-optimized marker can save significant fabric, especially in high-volume production.
🧵 What Is a Marker?
In garment production, a marker is a plan—either on paper or in digital format—that shows the optimal arrangement of all the pattern pieces needed to produce a particular style. These pieces are laid out across the fabric’s width and length, guiding the cutting process. A tight and precise marker helps reduce scrap, which refers to unusable fabric left between pattern pieces.
🎯 Objectives of Marker Making
- Maximize fabric utilization
- Minimize waste (scrap)
- Maintain fabric grain accuracy
- Preserve design integrity
- Support mass production efficiency
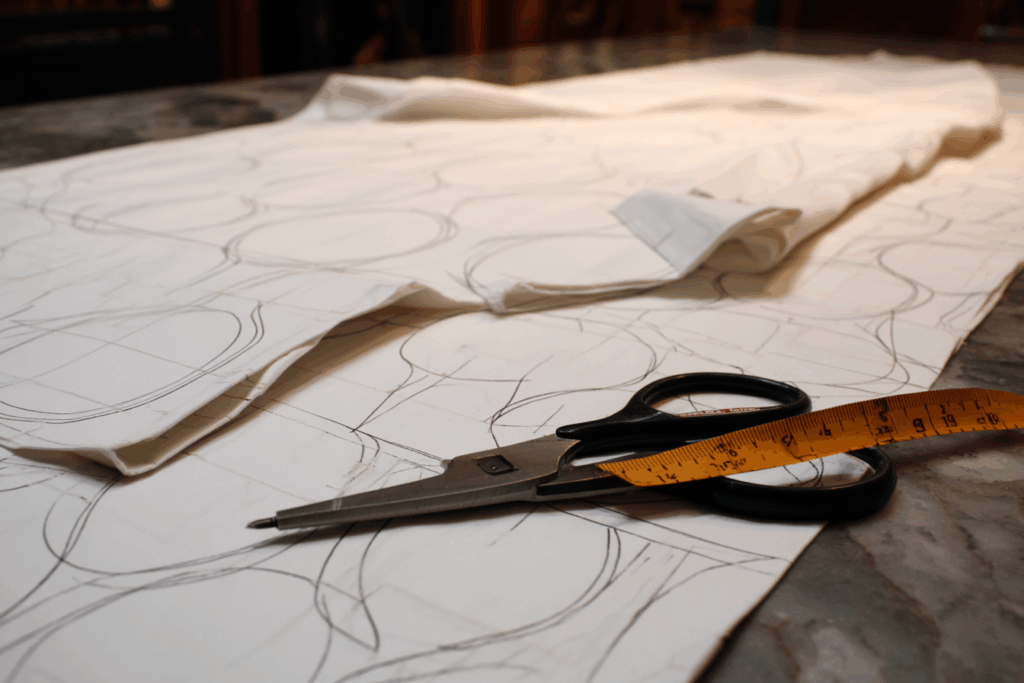
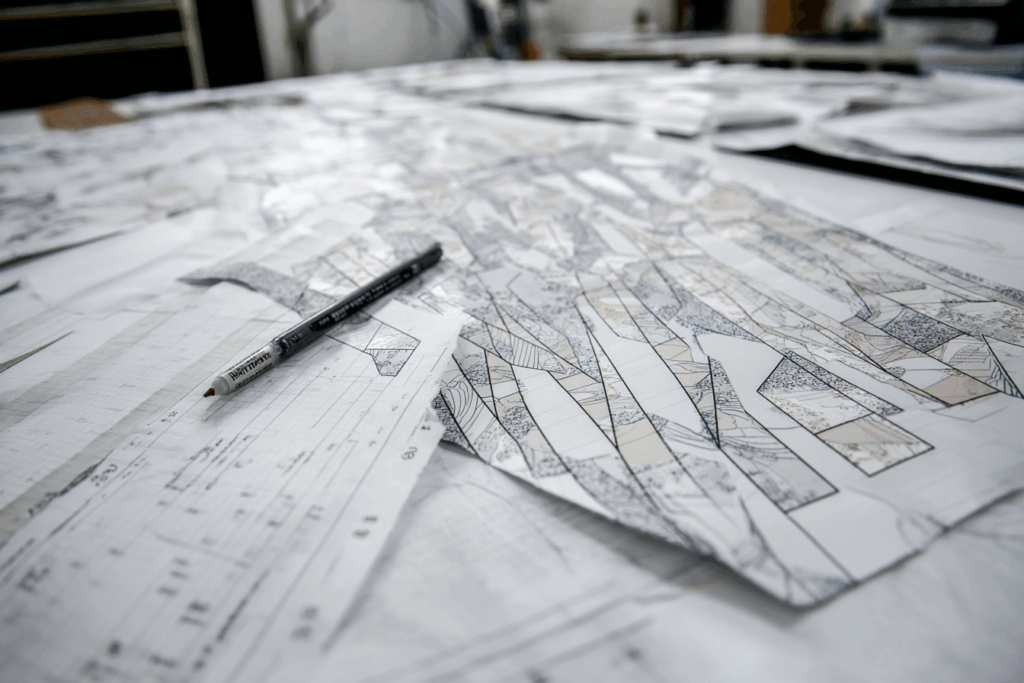
✂️ Manual vs. Computer-Aided Marker Making
Traditionally, markers were drawn manually on large rolls of paper. However, modern factories rely on CAD systems like Gerber AccuMark or PDS (Pattern Design System) to create digital markers. These tools allow technicians to:
- Replicate existing patterns
- Adjust layouts for different fabric types
- Save and retrieve versions for multiple garment sizes and styles
- Achieve precise measurements and consistency
📏 Key Considerations in Marker Planning
Factor | Description |
---|---|
Fabric Type | Solid fabrics are easier to mark; patterned or checkered fabrics require pattern matching. |
Grain Direction | Most main pieces must follow the straight yarn direction (warp) for drape and structure. |
Fabric Width | Marker must fit the narrowest usable width; some fabrics shrink during handling. |
Pattern Piece Size | Large and small pieces must be arranged like a puzzle to reduce gaps. |
Cutting Margins | Space is left at edges to avoid distortion during cutting. |
Bias Adjustment | Invisible or small pieces can sometimes have a slight weft bias to optimize space. |
🔄 Fabric Scrap Rate
- Standard scrap rate: 10–15%
- Optimized rate in bulk cutting: As low as 1%
This may seem minor, but for thousands of yards, these savings are significant.
📦 Marker and Layup: From Plan to Production
A layup refers to a stack of fabric layers to be cut simultaneously based on the marker. Markers are created for every fabric layer involved—outer fabric, lining, interlining, etc. The marker ensures:
- Pattern pieces align with fabric grain (especially the warp direction)
- Minimal deviation from true straight lines
- Consistent fit and finish
📌 Marker Efficiency Tips
- Use software to auto-nest pieces for optimal layout
- Group pieces by fabric type and production batch
- Analyze fabric consumption and revise frequently
- Allow tolerances for shrinkage and lay distortion
- Train staff in digital marker reading and editing
🏷️ Conclusion
Marker making plays a vital role in garment production. A well-prepared marker not only improves fabric yield but also ensures quality control, accurate sizing, and cost savings. With the rise of digital marker systems, today’s garment factories can enhance production planning and efficiency across all product lines.