Pushing Board: The Key to Sizing Consistency in Fashion Design
In the world of fashion design, ensuring that a garment fits well across multiple sizes is crucial. One of the key processes in achieving this is known as the pushing board or pattern grading. This technique allows designers to scale a sample size pattern up to larger sizes or down to smaller ones while maintaining the integrity of the design’s proportions. Whether for women’s or men’s clothing, pushing board ensures that a brand’s sizing is consistent, no matter the garment style.
What is a Pushing Board?
A pushing board is the process used to scale a sample size garment pattern either up or down. This is achieved through a technique called grading, where the pattern is proportionally enlarged or reduced to fit different size ranges, from size 4 to size 20, for example. The pattern is marked with various sizing increments, allowing manufacturers to create multiple sizes from a single sample size.
In figure below, we can see a piece pattern (right front piece) with all sizes stacked together—this is referred to as a nested combination. While the sizes may look similar, the grading increments (typically multiplied by 4 for front and back pieces) ensure that the design remains consistent across all sizes.
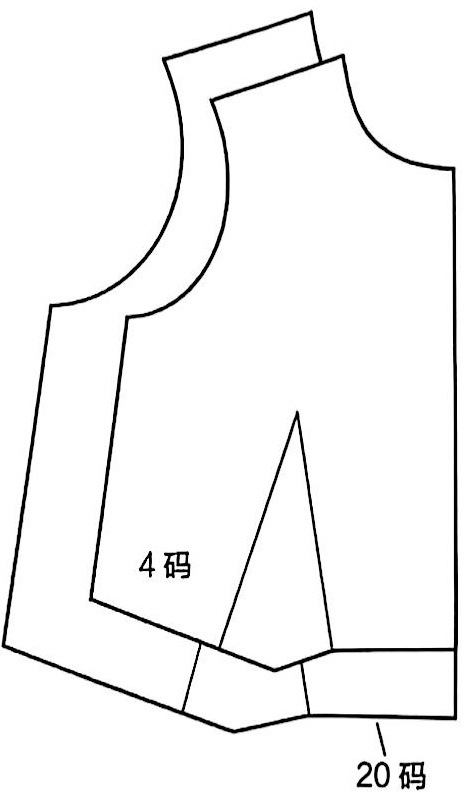
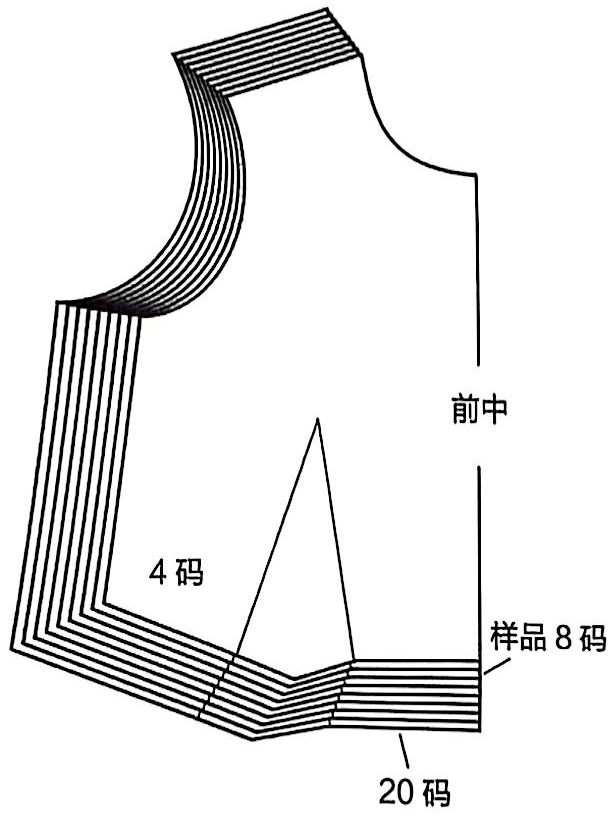
Purpose of the Pushing Board
The pushing board process follows grading rules, which are slightly different depending on the brand. However, all companies use the same sample sizes and grading rules to maintain sizing consistency. This means that if a customer wears a size 18 in one piece of clothing from a brand, they should be able to wear a size 18 in all of the brand’s clothing styles.
Another key purpose of the pushing board is to maintain the proportions of the original style. If defects exist in the sample size pattern, these may be amplified or concealed during the grading process. Therefore, it’s essential to calibrate the sample size pattern before starting the pushing process. This ensures that measurements such as pleats, cuts, alignment points, and yarn direction are accurate.
How Pushing Technology Works
Traditional Methods: Manual Pushing
In the past, the pushing board process was done manually. The garment pattern would be traced on a special cardboard after the size was determined. Then, each piece of the pattern would be slightly moved, and a new size would be redrawn. The finalized pattern would be transferred onto marker paper to create the cutting marker, which would then be used in garment production.
Modern Pushing Technology: Computerized Grading
Today, most factories use computer-aided design (CAD) systems to automate the pushing and marking of patterns. This technology allows for faster and more accurate grading. Many companies use a systematic push form template, which automatically fills in the remaining data based on the grading rules for a specific size.
The automation of the pushing process is particularly useful because it allows for consistency across all sizes. The grading system works by using body measurements and garment sizes, which are automatically applied to ensure a precise fit. Some styles, however, may require adjustments before pushing. For example, pants are typically sized with “all sizes are the same” pockets, ensuring that the pocket sizes remain consistent across sizes 8 to 16.
Real-World Applications of Pushing Board
Example 1: Pants Sizing
A common challenge with pushing board is ensuring that the design remains consistent, especially when dealing with complex garment features like pockets and waistbands. For example, in figure below, the pockets on pants are designed to be the same size for both size 8 and size 16. However, the loops (which attach the waistband) must be placed correctly to ensure that they don’t end too far apart. If the loops are too far from the center front, as shown in figure , the garment’s proportions may be off, leading to a poor fit.
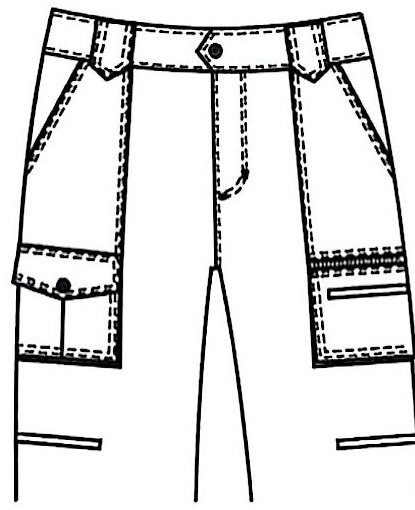
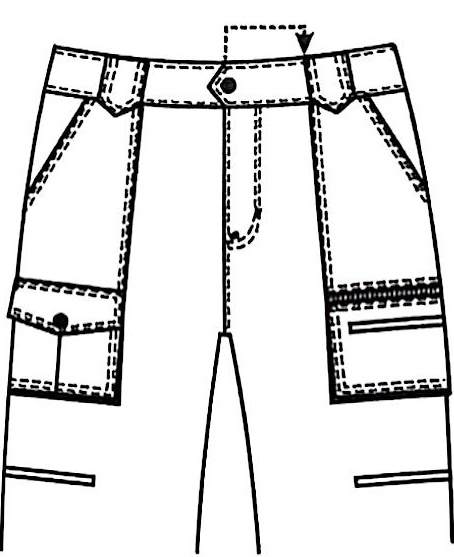
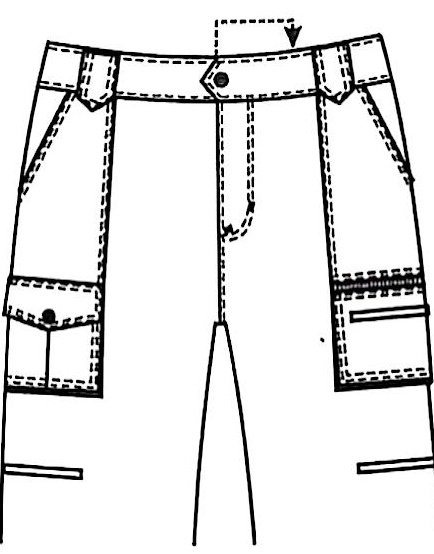
Example 2: Culottes Sizing
In another example, culottes (a type of short skirt with shorts attached inside) can show how grading can affect garment fit. In figure below, the exterior of the culottes is correctly sized, but the shorts inside are half an inch shorter than the skirt. If the standard sizing method is used for the shorts and not adjusted for the skirt, the result is that the shorts may end up longer than the skirt at larger sizes, as seen in figure . This discrepancy is undesirable and highlights the importance of correct grading for every detail in a garment.
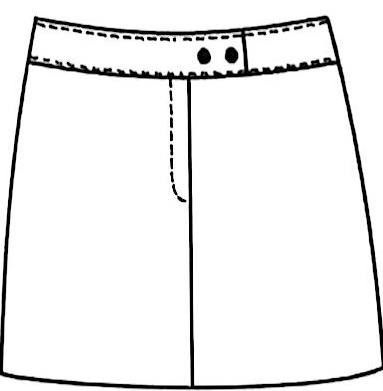
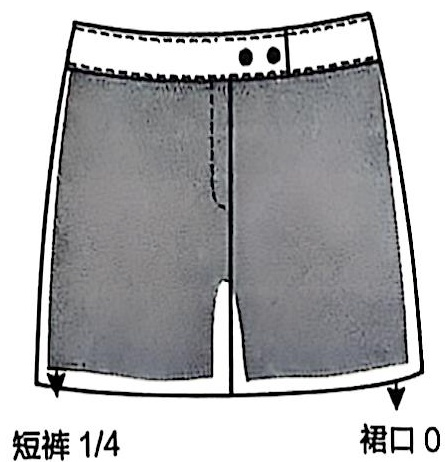
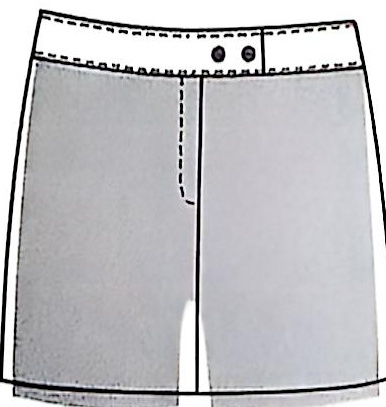
Why Proper Pushing Board Grading is Crucial
Pushing the plate or grading is straightforward for most patterns, but it requires careful analysis for individual cases. For instance, large size samples need to be checked on a fitting model to ensure that the pushing and grading are accurate, especially when it comes to proportions like waist-to-hip or bust-to-waist measurements. If the grading process is not done correctly, the garment may not fit properly in larger sizes, leading to production problems and customer dissatisfaction.
By using larger-size samples for production testing, companies can ensure that the pushing board process is suitable and avoid any potential issues before mass production begins.
Conclusion: The Importance of Pushing Board in Fashion Design
The pushing board process is essential for ensuring that clothing fits well across multiple sizes while maintaining the original design’s proportions. Whether done manually or using advanced computer technology, grading ensures consistency and accuracy in garment production. By automating much of the pushing process, fashion brands can save time and improve the accuracy of their patterns, but manual checks are still necessary for more complex designs.
In today’s competitive fashion industry, using the right pushing board technique is key to offering high-quality, consistent sizing across all garment types and sizes, from small to plus sizes. Properly scaled garments provide consumers with a better fit, enhancing brand loyalty and reducing returns. As the demand for better fitting clothes grows, so does the importance of perfecting the pushing board and grading processes in garment production.